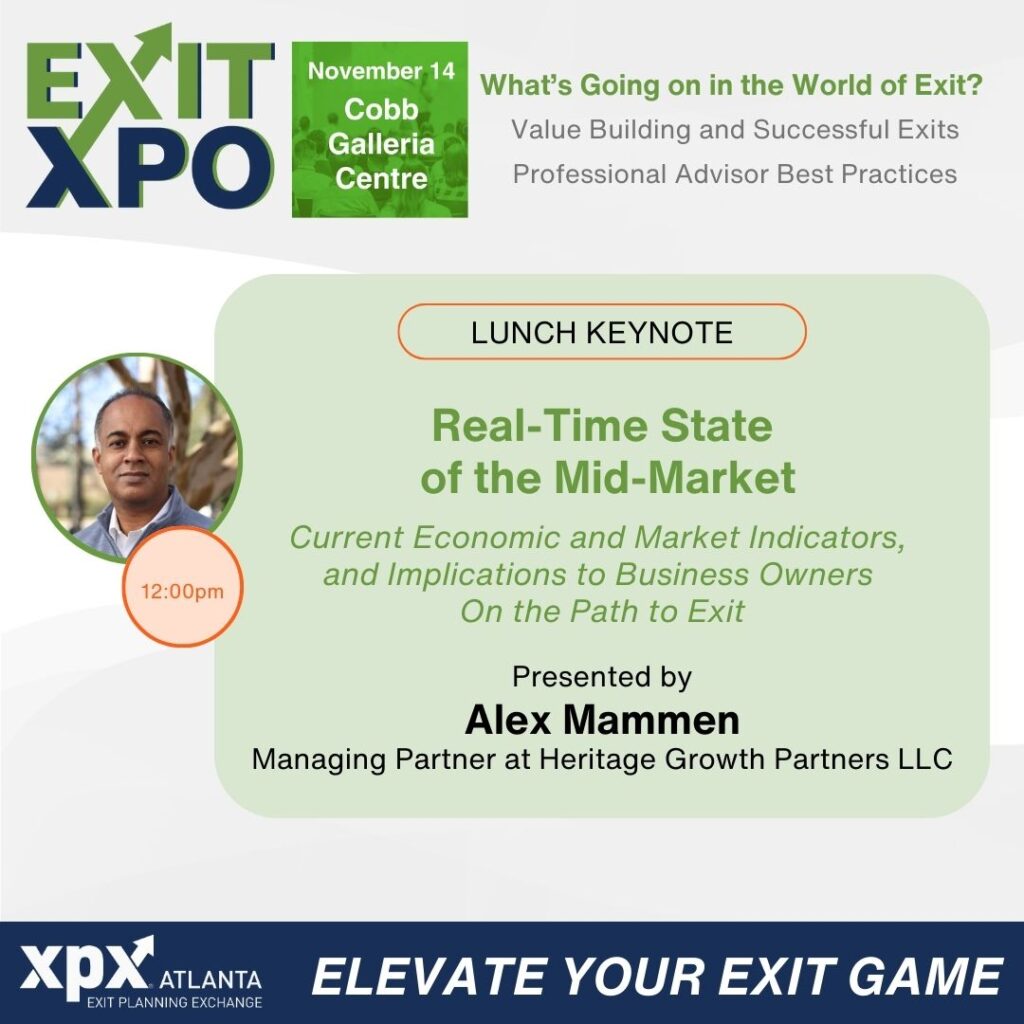
Alex Mammen Speaks at XPX Atlanta 2024 Exit EXPO Event
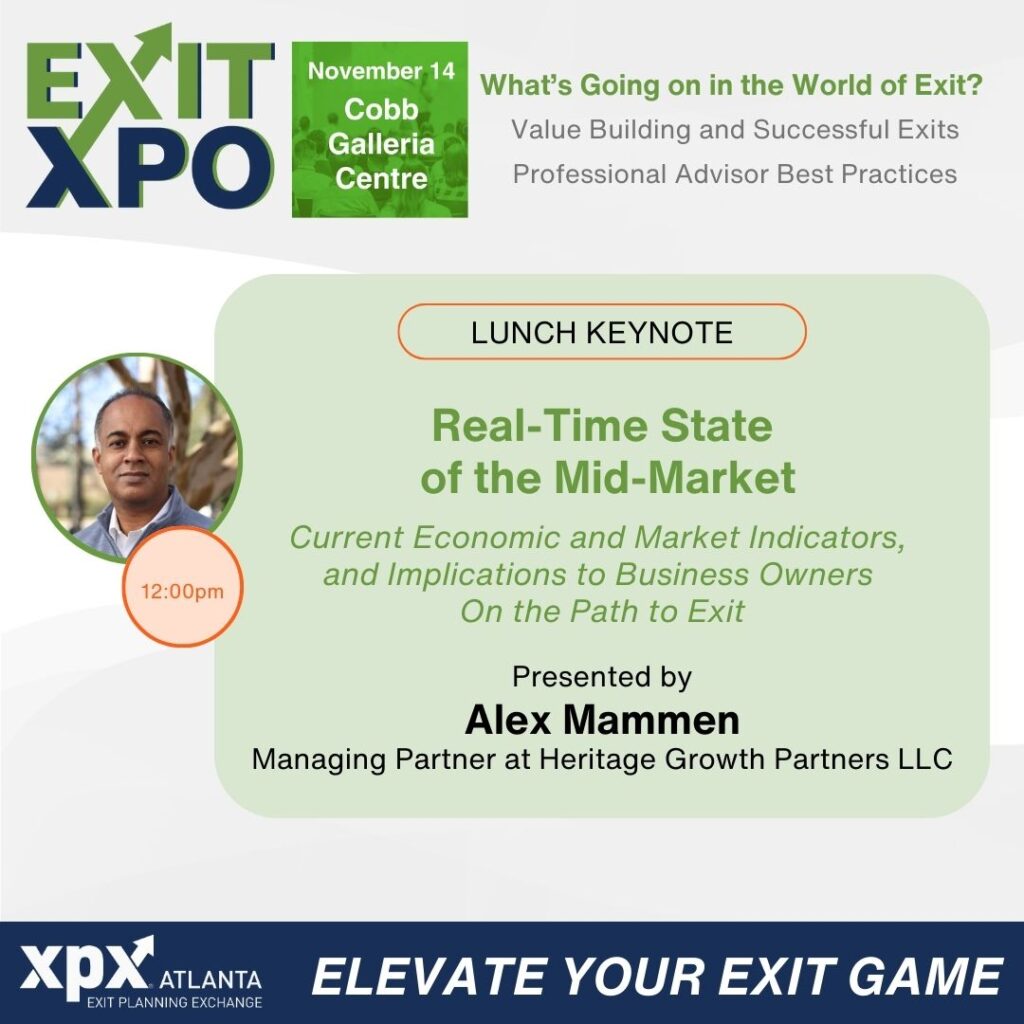
CAB Worldwide, one of our partnership companies, realized long ago that geopolitical issues and rising costs would make it challenging to manufacture in China.
As global markets evolve and the demand for more resilient and cost-efficient supply chains increase, equipment manufacturers are increasingly considering India as a critical strategic sourcing base. With 25+ years of experience in India, a large in-country team, extensive and diverse networks of established supply chain partner relationships and proven strategies in supply chain management, CAB Worldwide stands out as the optimal partner for the transition to India.
This brief document provides details on CAB’s expanded design, engineering and production capabilities in India.
TAMPA, FL (August 19, 2024) — The Environmental Graphic Design (EGD) Studio at Creative Sign Designs is pleased to announce the addition of Amy Gullickson — who has spent the last decade developing wayfinding signage systems and creating efficient and consistent processes across multiple, dynamic design teams.
In her new role, Amy will manage all internal and external EGD project timelines as well as oversee quality control for the department. Additionally, Amy will be tasked with evolving the standard operating procedures within the department to better support client needs.
“We are excited to elevate our approach and demonstrate increased responsiveness to clients’ needs through the expansion of our EGD Studio,” said Jamie Harden, President and CEO at Creative Sign Designs. “This expansion, supported by Amy’s experience and expertise, is going to enhance our clients’ creative visions – by bringing streamlined processes and technologies to the forefront, capitalizing on all opportunities to feature client originality.”
The Environmental Graphic Design Studio exists to bring each client’s vision to life in a way that enhances the visitors’ experience: leaving a positive, lasting impression. The studio was created in 2018 and has since worked on projects like Feeding Tampa Bay, USF Honors College, Hewanorra International Airport and Renata at Lakewood Ranch. Having an EGD studio in-house has allowed CSD to streamline the design process, particularly during the initial phases of a project.
Alongside the hiring of Amy, Alicia Hanson, is transitioning into a new role as EGD Studio Creative Lead. Alicia is a 25-year EGD veteran and will provide creative direction for the studio moving forward: overseeing all aspects of the design process from Concept Creation to Design Development. In addition, Alicia will be responsible for developing and maintaining the vision for the studio, ensuring all projects are aligned with client’s overall aesthetic and brand identity.
“During her time with us, Alicia has already demonstrated an unmatched ability to bring creative visions to life,” said Adam Wold, Director of Project Development at Creative Sign Designs. “We look forward to her continued growth here and are excited to see the new projects she touches in the studio.”
In her efforts, Alicia will also support Amy to ensure quality control across all EGD Studio output. Both Alicia and Amy will report to our Director of Project Development.
To meet the EGD team and learn more about our capabilities and work, please contact Creative Sign Designs.
TAMPA, FL (July 15, 2024) — Creative Sign Designs, a leader in branding, wayfinding and architectural signage solutions, today appointed a new Chief Financial Officer, Josh Baldwin. Josh brings with him 21 years of experience along with an integrous attitude poised to maintain the company’s strong financial operations. Paul Wilbur, the prior CFO will be relocating for personal reasons, but will remain with Creative in a newly created Chief Administrative Officer role.
“Josh joins us with a wealth of knowledge in his field, and I know he will be a true asset to our company,” said Jamie Harden, President and CEO of Creative Sign Designs. “Our last CFO was with the company nearly two decades, and we expect Josh will create another long-time employee in this position.”
Josh comes to Creative Sign Designs from Ball Corporation, where he rose in the ranks from the Plant Accountant to Regional Controller until he transitioned to SteriPack Medical Contract Manufacturing as the U.S. Director of Finance. He has also been greatly involved with Trax Credit Union for more than 10 years and currently serves as the Vice Chairman. At Creative Sign Designs, Josh will handle the strategic financial management of the company through managing the following: Financial Reporting Analysis, Treasury Management, Mergers and Acquisitions activity, Banking and Investor relations and Audit/Tax.
The last time a CFO role was open at Creative Sign Designs was 18 years ago, before Paul Wilbur sat in the position. As CAO Paul will continue to play an integral role on the executive leadership team, helping steer the strategic vision of company operations.
“The CFO role here has always been critical,” said Harden. “We truly rely on this individual to advocate for the financial well-being of our company while keeping us in line with budgets and capital planning, supporting our sales and operations teammates while ensuring the overall fiscal health of Creative Sign Designs. We know Josh will provide a solid and dependable discernment of the financial operations of our company.”
Josh joins a highly experienced, tenured and successful executive team at Creative Sign Designs and will work alongside the support of Heritage Growth Partners, an Atlanta based private, family investment office that partnered with Creative Sign Designs in 2021
You may be wondering why we chose the topic of outsourced manufacturing for our inaugural edition of “Planting Seeds”. Very simple – since the founding of our firm in 2014, outsourced manufacturing has been a consistent theme that we have seen across a wide range of industries and business types. Additionally, Heritage Growth’s prior and current investment partnerships range from businesses providing comprehensive outsourced manufacturing services to companies benefiting from the ability to outsource their manufacturing. Despite mixed political and economic messages on the topic, we believe trends continue to reinforce the ongoing growth of outsourced manufacturing which bodes well for future investment.
History and Outlook
Outsourced manufacturing, similar to other types of outsourcing, was primarily viewed as a way to cut costs by outsourcing simple, low-value commodity products and services. However, over the last 25 years, outsourced manufacturing has evolved to provide a variety of additional strategic benefits to businesses. These include greater flexibility and scalability, increased diversification and specialization of capabilities, improved visibility, better resource utilization and increased profitability. As a result, outsourced manufacturing has become a pervasive force. According to a comprehensive study by Data Bridge Market Research, the global outsourced manufacturing market is expected to grow at a CAGR of 6.95% through 2029.1 This projected expansion, particularly at a rate in excess of expected overall economic growth, underscores the ongoing prominence of outsourcing as a strategic imperative for manufacturers worldwide and highlights favorable tailwinds for the industry.
Drivers of Outsourced Manufacturing
Companies continue to recognize that creating mutually beneficial partnerships with parties that specialize in different parts of the value chain increases productivity and profitability. The attractiveness of this theme has also grown in the private and public markets, which reward companies for greater predictability, lower fixed investment and higher free cash flow. With speed to market becoming increasingly important, Original Equipment Manufacturers (“OEMs”) increasingly rely on outsourced manufacturers who “bridge the divide between concept and manufacturability… [and] manage the process from concept to production. 2 An experienced outsourced manufacturer is “more adept at understanding how to reduce manufacturing complexities and improve processes and operations.”3 With the focus and know-how to navigate disrupted supply chains and innovative technologies to manage workflows, outsourced manufacturers can scale operations to meet customer volume demands while also addressing the regulatory complexities of the market. Additionally, the shift from relying on internal staff to outsourcing partners has led to increased expenditure accountability as OEMs now enjoy more transparency and control over costs, ensuring efficient resource allocation and cost optimization.
Companies are also outsourcing manufacturing to shift further towards an asset-light business model. Once seen as a strategy only used by underperforming companies, the asset-light model is increasingly seen as the gold standard for long-term growth and higher shareholder returns. 4 Here are three examples of how an asset-light model, driven by outsourced manufacturing, supports greater return on capital:
When researching U.S. Fortune 500 public companies, Ernst & Young LLP found that asset-light companies – “those that have an average five-year Property, Plant and Equipment to sales ratio lower than their respective sector mean” – outperformed their competitors by an average of more than four percentage points on shareholder returns in the last five years. The greatest spread in outperformance was seen in the manufacturing industry, which is traditionally known for its high capital expenditure spending and asset-heavy balance sheets.6 In response to an “increasing need for innovation, maintaining liquidity and building more agile and resilient operating models,” companies are outsourcing manufacturing and opting for asset-light business models that bring strategic improvements to production processes while benefitting from a higher valuation on Wall Street. 7
Finally, with the aging workforce and the projected continual decline in the U.S. population without immigration8, domestic manufacturers benefit from the ability to leverage the skilled and focused labor forces offered by outsourced manufacturers. Specialized outsourcing processes and roles ultimately allow manufacturers to re-focus existing employees on more high-value roles, leading to improved operational efficiency, increased profits and lower turnover through greater employee satisfaction.
Implications for Outsourced Manufacturers
Whereas companies traditionally resorted to offshoring primarily to China due to its well-developed supply chains, disruptions brought on by the pandemic and increased geopolitical uncertainty have emphasized the importance of diversifying supply chains and developing a mix of onshore, nearshore and offshore partners. With companies seeking to diversify their supply chains and the related complexity, businesses are seeing a growing need for specialized, ideally domestic partners to manage this transition and oversee a more complex, global network.
For outsourced manufacturers seeking to maintain a competitive edge, the emphasis has shifted toward providing turn-key solutions from front-end design/design for manufacturing (“DFM”) services to post-production distribution, inventory management and logistics support. In addition, consolidation continues in the industry as larger outsourced manufacturers can offer greater buying power and other economies of scale to their clients to improve profitability and drive down product costs to increase market acceptance. Being a full-service outsourced manufacturer and having the benefits of scale have emerged as important strategic advantages compared to being just a low-cost subcontractor solely focused on manufacturing. The ability to offer a range of services beyond production bolsters an outsourced manufacturer’s value proposition, ensuring sustained relevance and resilience, especially during challenging times. 9
Customer concentration is a typical and real risk that outsourced manufacturers bear as their OEM clients ask them to take on more work. However, when managed properly, this risk may in fact be a path to long-term success as outsourced manufacturers cultivate sticky partnerships with OEMs that span the value chain from design to manufacturing to distribution and expand across multiple product lines. Through diverse capabilities that drive innovation and create customer-centric, turn-key solutions, high-performing outsourced manufacturers can evolve their OEM relationships into critical, long-term business partnerships with attractive margins.
Heritage Growth’s Outsourced Manufacturing Experience
Heritage Growth is currently partnered with the management team of CAB Worldwide (“CAB”). Founded in 1982, CAB is a Georgia-based provider of global engineering, DFM, production and supply chain management services, with a focus on cast, forged and fabricated steel, iron and aluminum precision components and assemblies. As a result of increased demand from OEMs seeking to diversify their domestic and global supply chains, CAB’s customer base has expanded particularly due to CAB’s expertise in India where the business has operated for 20+ years.
Heritage Growth is currently partnered with the management team of Creative Sign Designs (“CSD”). Founded in 1986, CSD is a Florida-based provider of consulting, design, manufacturing and installation services for interior and exterior signage. CSD has seen consistent growth through a hybrid model of in-house production and outsourced manufacturing. Through the development of strategic partnerships with a network of qualified domestic, nearshore and offshore manufacturers, CSD has been able to expand its product assortment and scale production capabilities beyond internal capacity limits, and ultimately increase market competitiveness and customer reach. CSD utilizes a similar hybrid approach for its installation services by self-performing sign installations within a 200-mile radius of its Tampa, FL and Orlando, FL manufacturing facilities and outsourcing installation to a network of providers in other markets.
Heritage Growth was previously partnered with the management team of East West Manufacturing (“East West”). Founded in 2001, East West is a high-growth provider of onshore, near shore and offshore design, engineering, manufacturing and distribution services focused on the full spectrum of customer needs ranging from new product design to full scale production and distribution. East West has maintained its competitive advantage by utilizing a global design team, transparent supply chain, on-site quality control and flexible logistics systems.
——
We hope you found this edition of “Planting Seeds” interesting and helpful. As always, we welcome your feedback and please reach out to any of us if we can be of assistance. info@heritagegrowth.com.
Jamie Harden is President and CEO of Creative Sign Designs. Creative employs more than 140 people throughout the state of Florida with the majority based at its Tampa headquarters.
Creative Sign Designs is one of the largest sign companies in the Southeastern United States. Creative provides consultation, design, project management, fabrication, and installation services for a full range of interior, exterior and digital signage products.
Creative has won numerous important accolades including:
Prior to purchasing Creative Sign Designs Mr. Harden spent 15 years in various senior leadership roles with Bank of America in Tampa, Kansas City, Dallas and Los Angeles.
Education
Mr. Harden is a graduate of Florida State University with a Bachelor of Science in Finance.
Professional and Community Affiliations
Jamie has been married to Melanie Turner Harden, also a Florida State University College of Business graduate, for more than 30 years. They are very proud parents of the three Florida State University students – Battle (21), Ellee (18) and Turner (18).